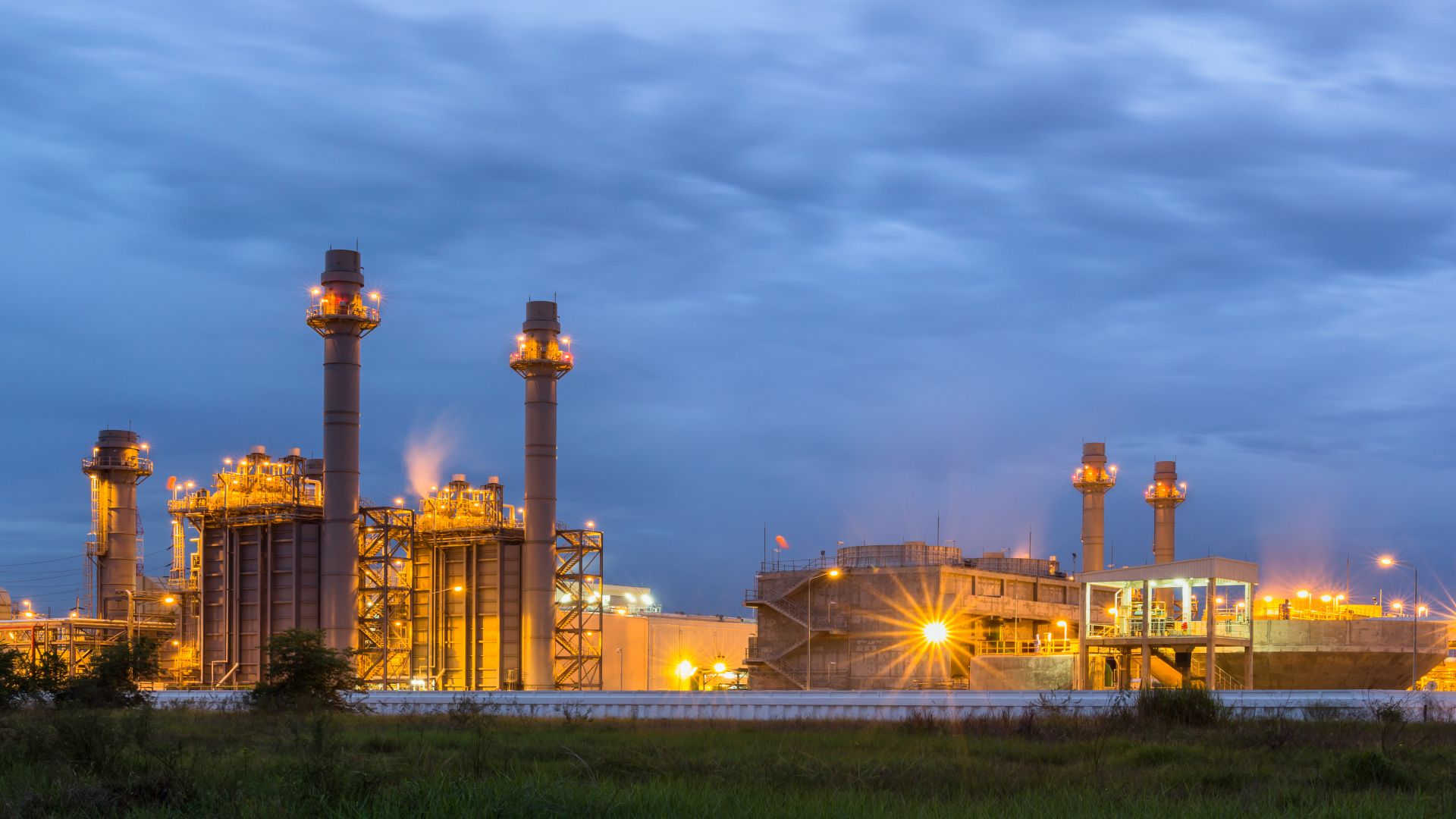
Innovating
Technology
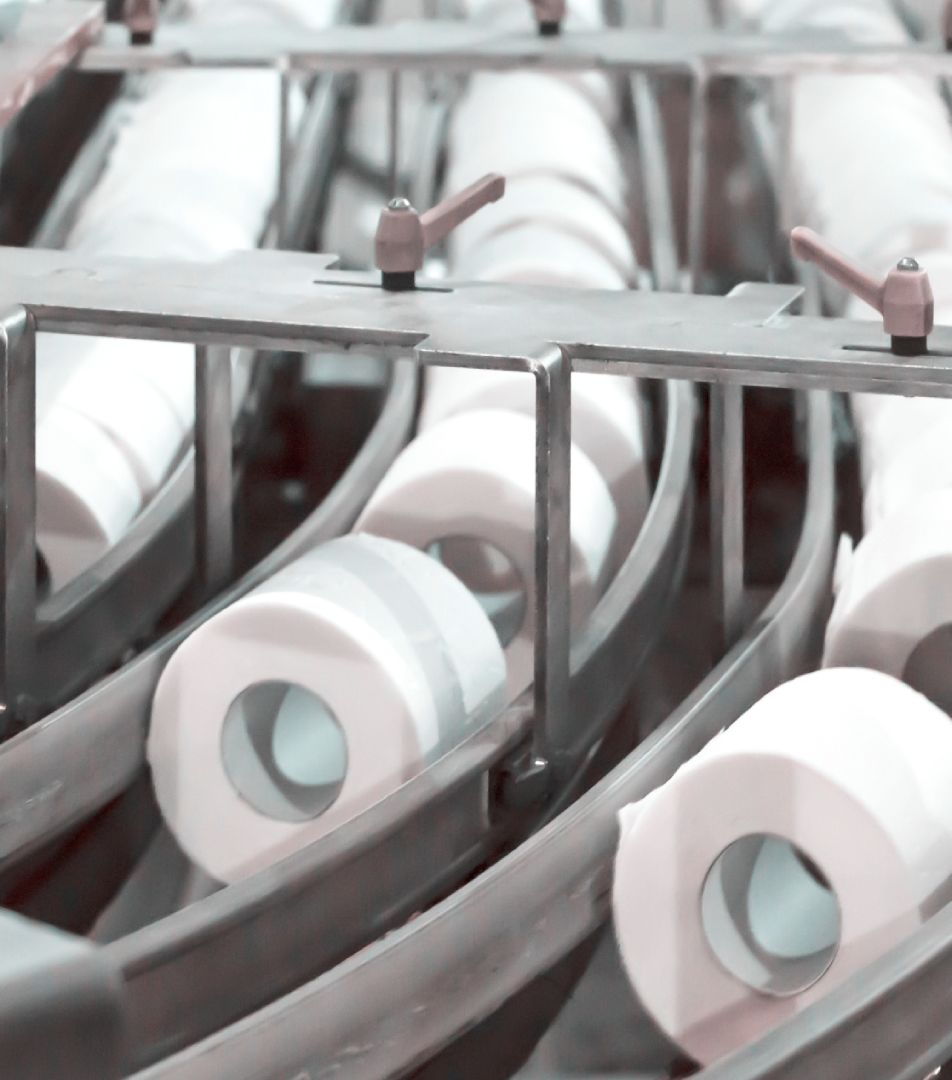
Pulp & Paper
Simply generating steam at process pressure instead of high pressure to generate power at the top end has a lost opportunity cost. Conversely, steam at ordinary process heating conditions still has a considerable amount of enthalpy that could be used for power generation, so cogeneration also has a lost opportunity cost. The high cost of grid power directly affects the bottom of paper industries, and the best option that manufacturers have is to install their own captive power plants, which will operate in cogeneration mode. The capital and operating cost of high-pressure boilers, turbines and generators are substantial and this equipment is typically operated continuously which usually limits self-generated power to large-scale operations.
An array of Steam Turbine designs and performance capabilities are offered to match desired specifications. The turbine develops the appropriate balance between power and steam to maximise the potential of the cogeneration process, thereby minimising the impact on the environment. We have delivered over 75 optimally designed steam turbo-generators which not only deliver power but also lead to a consistent steam flow for the process.
A typical power generation turbine in a paper mill may have extraction pressures of 11 kg/cm2 and 4 kg/cm2. Typical Backpressure may be 4 kg/cm2. In practice, these pressures are custom designed for each facility. The extracted or exhaust steam is used for process heating, such as drying paper, evaporation, heat for chemical reactions or distillation.
Contact Reach out to us
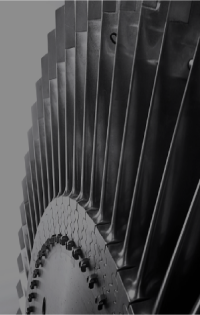