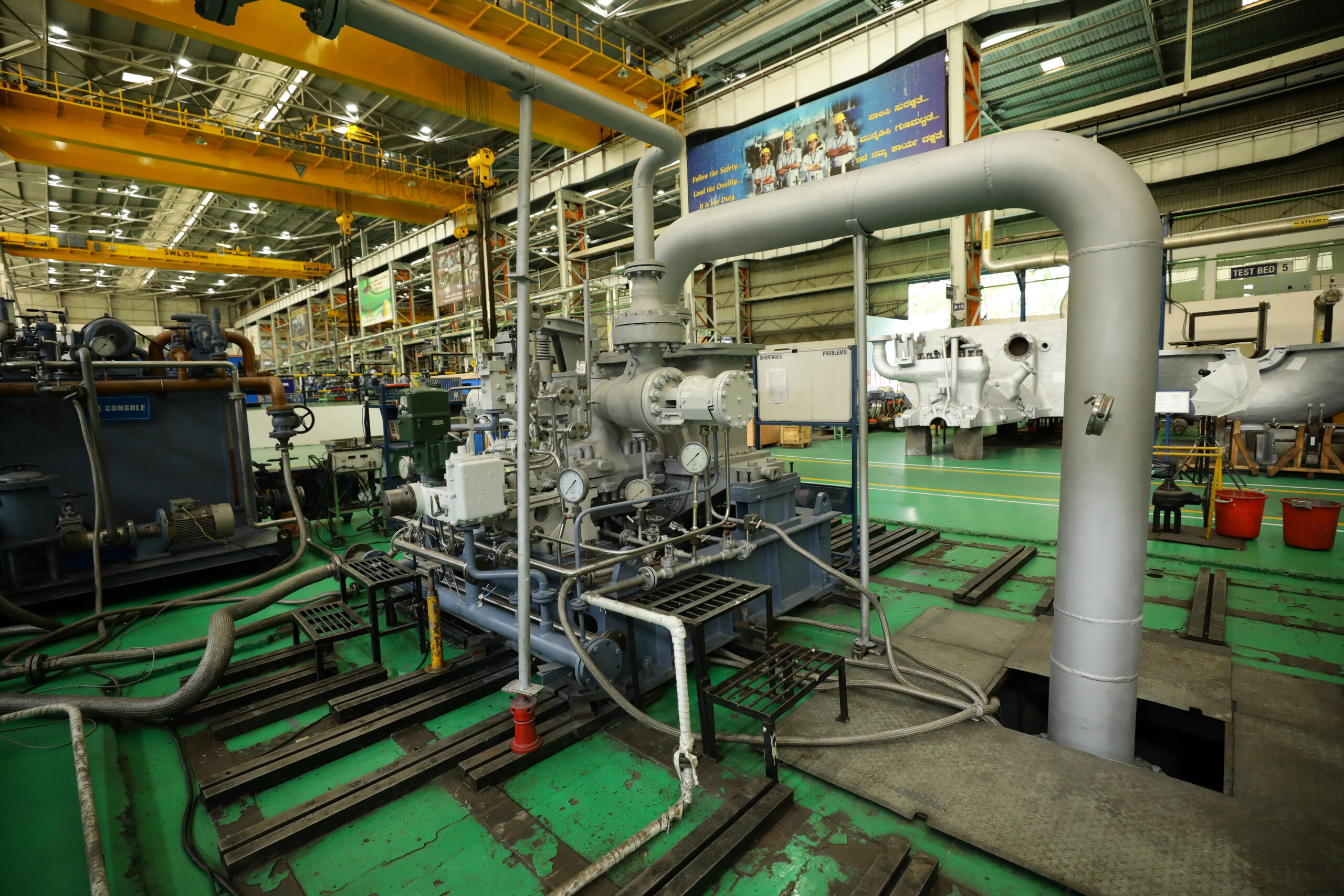
What are the Best Ways for the Maintenance of Steam Turbines?
Steam turbines are crucial for power generation in industrial captive power plants, independent power producers (IPPs), and geothermal power stations. However, without proper maintenance of steam turbines, their efficiency, reliability, and lifespan can be affected, resulting in unexpected downtime and increased operational costs.
At Triveni Turbines, we understand that maximizing steam turbine performance requires a proactive and well-structured maintenance approach. By adopting best practices such as routine inspections, lubrication system checks, vibration monitoring, and predictive maintenance, plant operators can prevent costly repairs, enhance energy efficiency, and ensure seamless, uninterrupted operations.
Routine Inspections and Cleaning
Routine inspections are essential for identifying early signs of wear, misalignment, or component damage in steam turbines. Regular cleaning prevents the accumulation of deposits on turbine blades, which can hinder performance and reduce efficiency. Keeping the system clean ensures seamless operation and helps maintain high-efficiency steam turbines.
Lubrication Systems Maintenance
Effective lubrication reduces friction between moving parts, preventing overheating and excessive wear. Regularly monitoring and maintaining optimal lubrication levels is crucial. Timely oil filter replacement and thorough inspection of the entire oil circuit further enhance the steam turbine’s reliability and efficiency.
Vibration Monitoring
Monitoring vibration levels is crucial for identifying imbalances or misalignments in steam turbines. Utilizing advanced vibration analysis techniques helps detect potential issues during early stage, enabling proactive maintenance and minimizing the risk of unexpected downtime.
Bearing Maintenance
Bearings play a vital role in supporting the steam turbine’s rotor. Regular inspection and maintenance of bearings ensure smooth operation. Utilizing condition-based maintenance approaches, such as operational technology integration, can improve bearing performance and extend its lifespan.
Predictive and Preventive Maintenance of Steam Turbine
Adopting predictive maintenance strategies for steam turbines involves real-time condition monitoring through advanced sensors. This approach enables maintenance activities to be scheduled before issues escalate, optimizing operational efficiency and minimizing downtime.
In contrast, preventive maintenance strategies focus on identifying potential issues before they lead to system failures. By regularly inspecting key components such as bearings, lubrication systems, and steam turbine blades, plant operators can maintain optimal performance and prevent unexpected downtime. This maintenance strategy includes vibration monitoring, pressure checks, and testing of control systems to detect any irregularities early, significantly improving overall reliability.
A comprehensive maintenance plan is essential for ensuring efficiency, reliability, and environmental sustainability. Routine inspections, proper lubrication, vibration monitoring analysis, and predictive maintenance are key aspects in preventing costly repairs and extend steam turbine’s lifespan.
At Triveni Turbines, we provide cutting-edge technology and customized solutions designed to enhance performance while reducing environmental impact. To learn more about our tailored power generation solutions, contact us today.