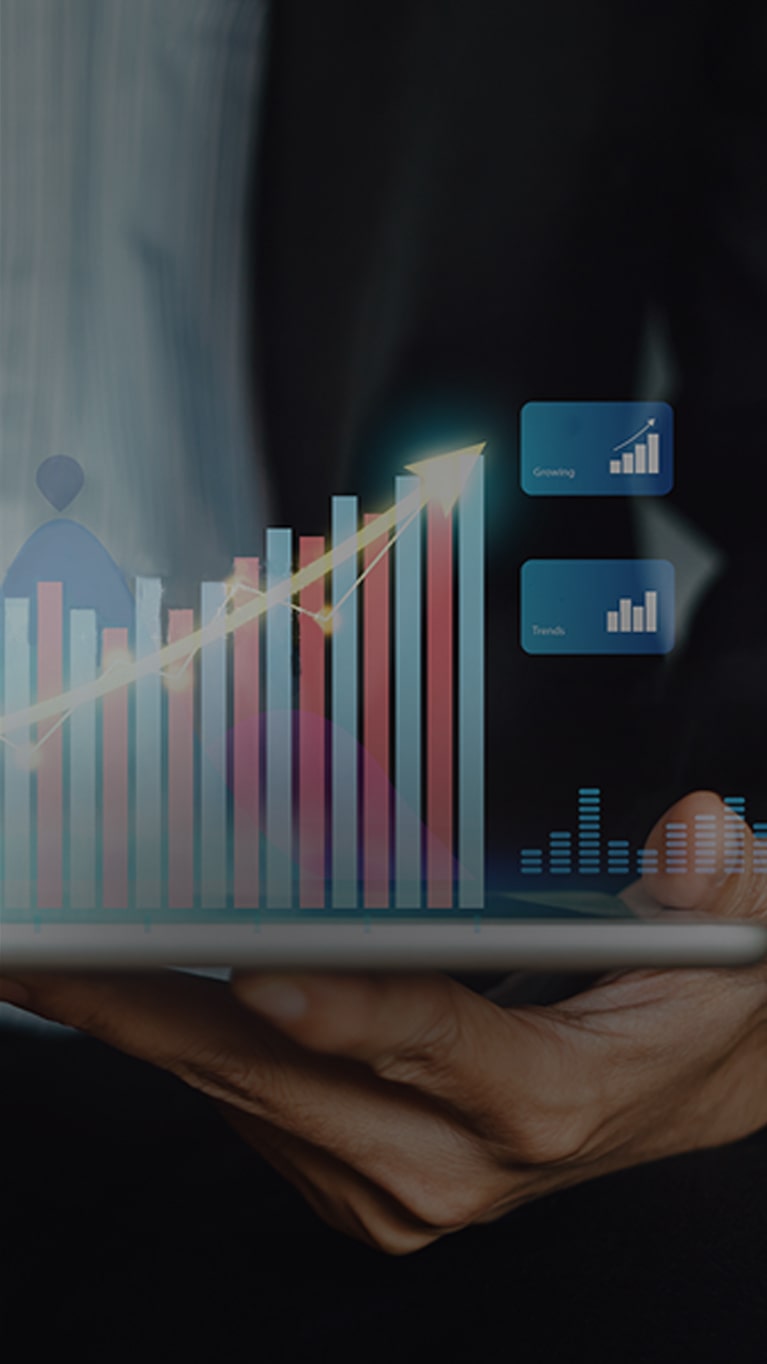
Inspired
Performance
Overview
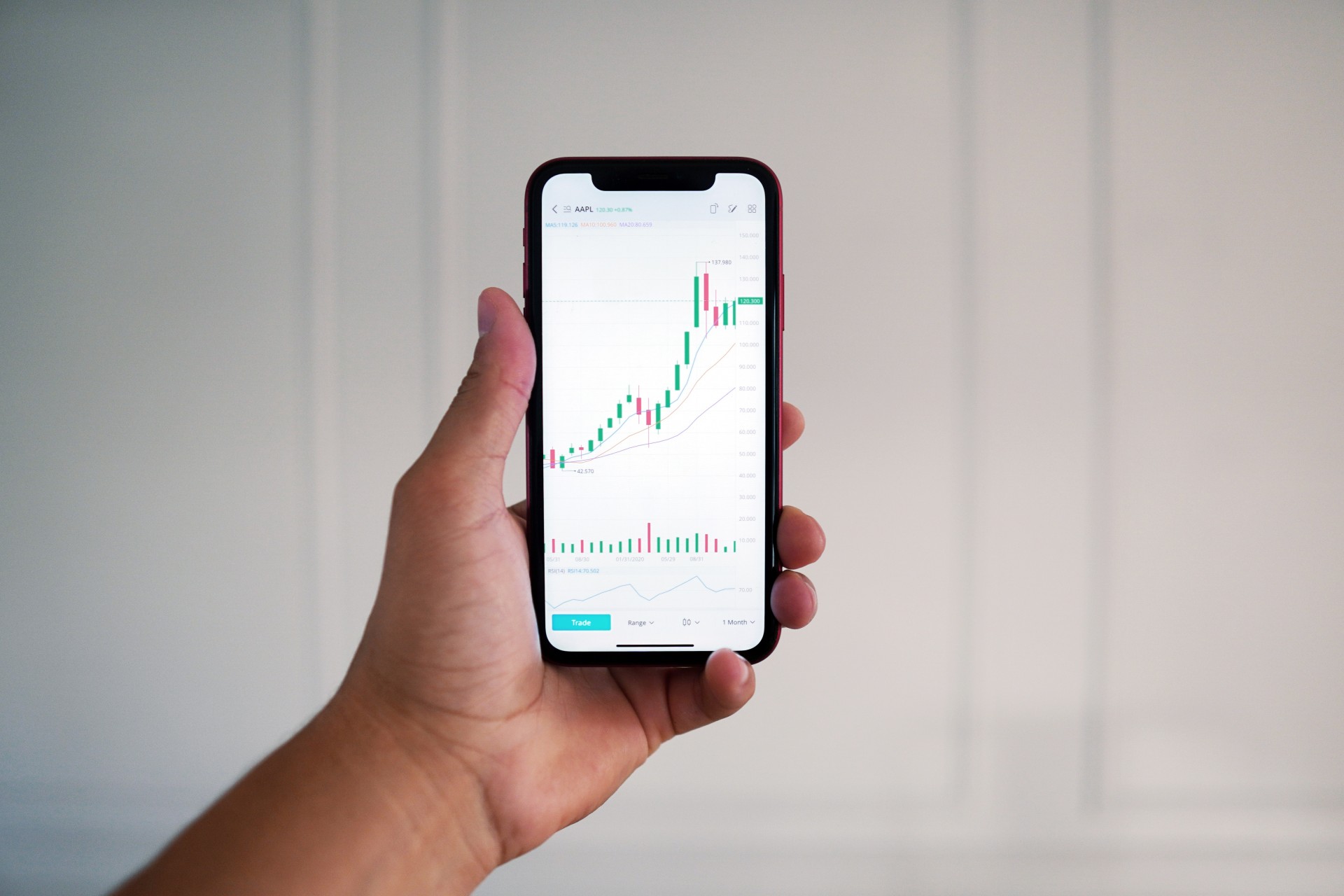
Triveni Turbine Limited is firmly dedicated to achieving sustainable growth and creating value in the long-term. We believe that in order to create shareholder value, we must address other stakeholders as well. In line with the above philosophy, our Company continuously strives for excellence through adoption of best governance and disclosure practices. Our Company recognises that good governance is a continuous exercise and thus reiterates our commitment to pursue highest standard of Corporate Governance in the overall interest of our stakeholders. Our Company also promotes a high level of transparency and accountability in internal and business conduct.
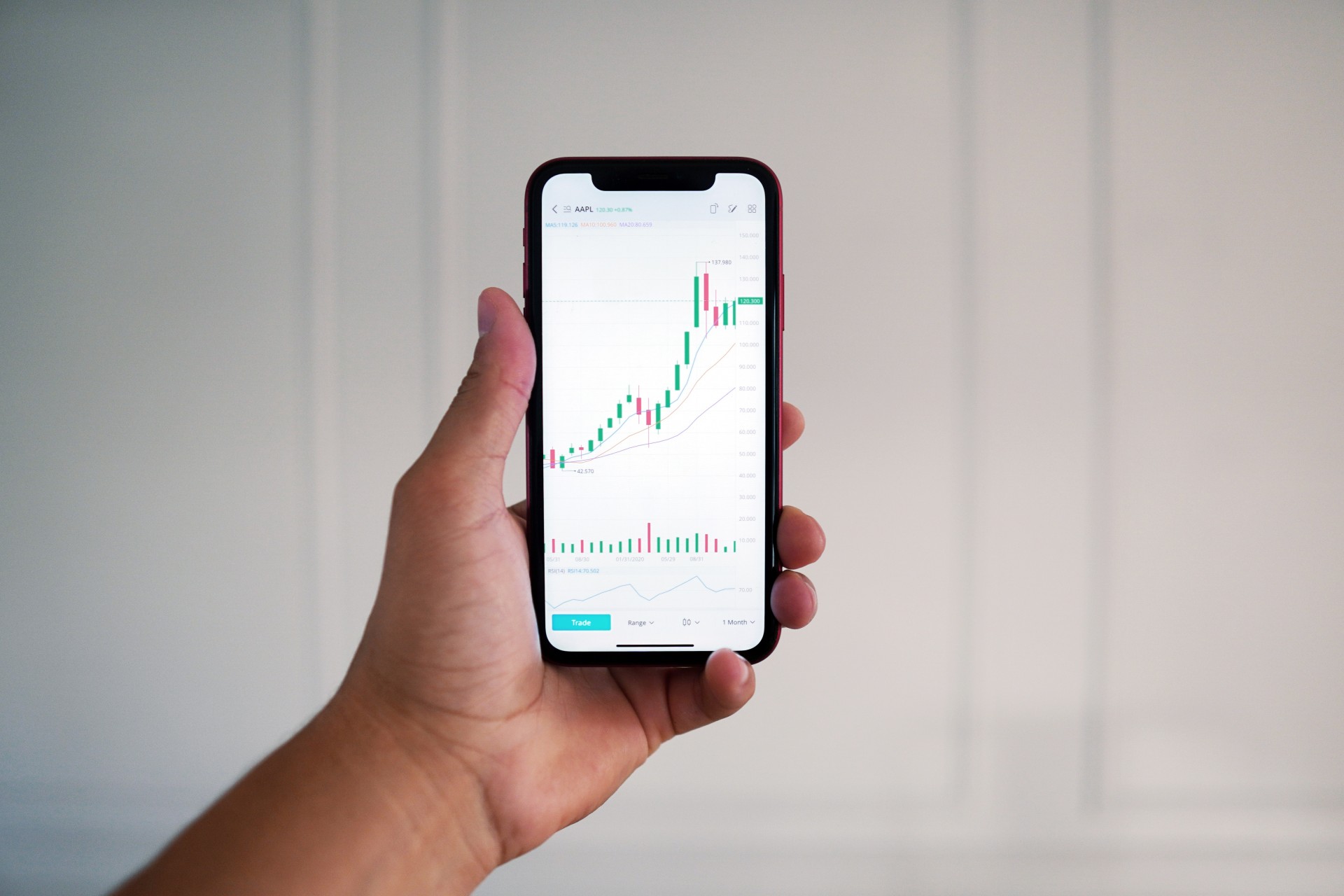
Investor Kit
Quarter-Wise
Performance FY25
Revenue from Operations
EBITDA
Profit Before Tax (PBT)
Profit After Tax (PAT)
*EPS (not annualized)
Outstanding order book
*Not annualised for the quarter
Revenue from Operations
EBITDA
Profit Before Tax (PBT)
Profit After Tax (PAT)
*EPS (not annualized)
Outstanding order book
*Not annualised for the quarter
Revenue from Operations
EBITDA
Profit Before Tax (PBT)
Profit After Tax (PAT)
*EPS (not annualized)
Outstanding order book
*Not annualised for the quarter
Revenue from Operations
EBITDA
Profit Before Tax (PBT)
Profit After Tax (PAT)
*EPS (not annualized)
Outstanding order book
Key Performance
Highlights
Shareholder Services
For grievance redressal and queries related to shares, please contact:
Corporate Office of the Company
Mr. Pulkit Bhasin (Company Secretary)
Triveni Turbine Limited
Phone: +91-120-4308000
Fax: +91-120-4311010-11
Email:cs.compliance@triveniturbines.com
Registrar and Transfer Agent
Alankit Assignments Limited (Unit: Triveni Turbine Limited)
Phone: +91-11-4254-1234
Email:cs.compliance@triveniturbines.com
Website: www.alankit.com
Investor Relations Contact
For institutional investors’ / analysts’ queries, please contact:
Ms. Surabhi Chandna
Investor Relations & Value Creation
Triveni Turbine Limited
Phone: +91 120 430 8000
Fax: +91 120 431 1010
Email: ir@triveniturbines.com