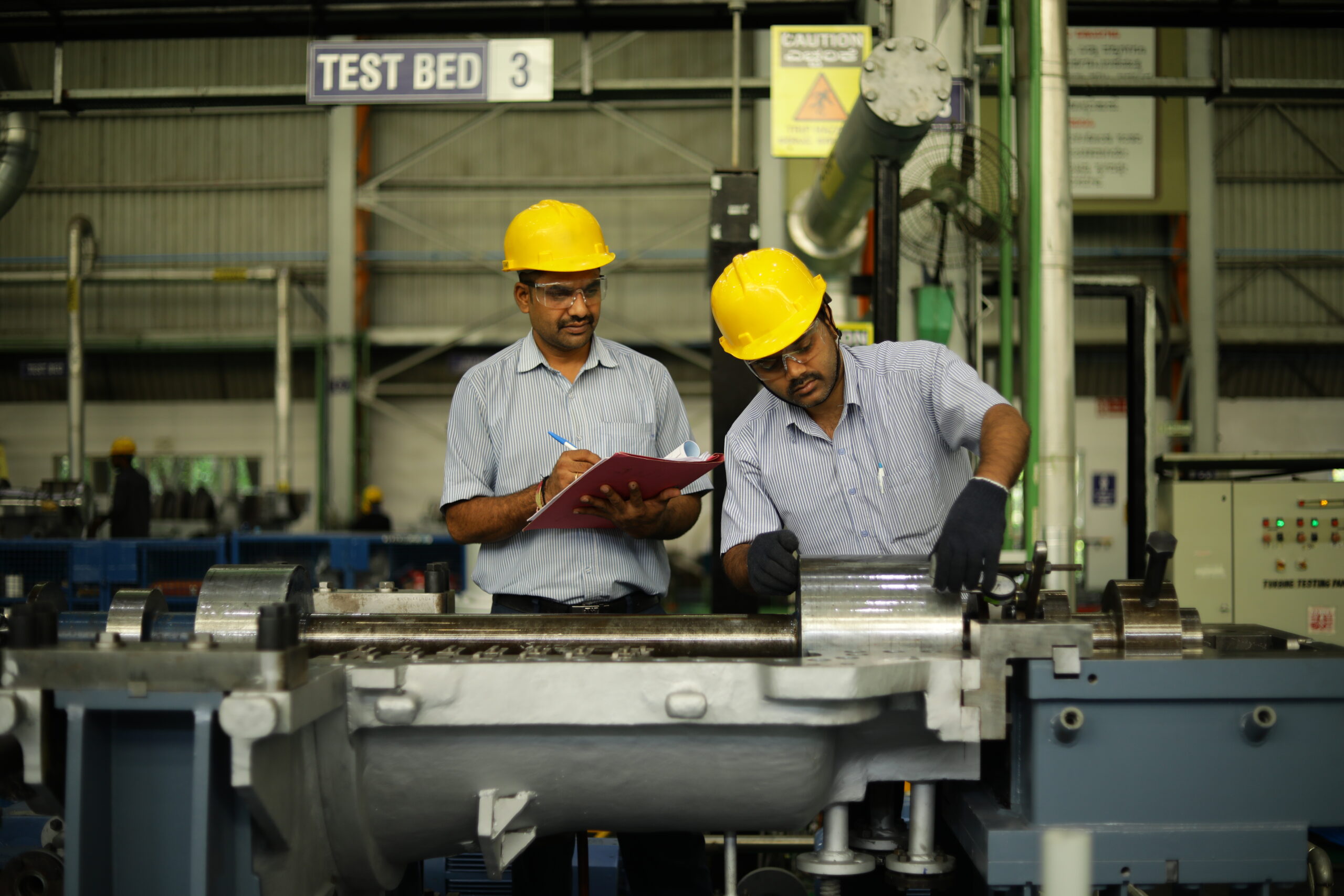
5 Top Challenges in Steam Turbine Repairs and How to Fix Them
Steam turbines are essential for power generation across Industrial Captive Power Plants, Independent Power Plants (IPPs), Oil & Gas Plants, Utility Power Plants, and Geothermal Power Plants. However, maintaining their efficiency and reliability requires proactive repair and maintenance strategies. Factors such as component wear, overheating, and vibration can affect performance and result in costly downtime.
This blog delves into the major challenges of steam turbine repair and highlights innovative solutions that are improving performance and sustainability.
Component Wear and Tear
Over time, steam turbines undergo wear and tear conditions in key components such as blades, rotors, and bearings. Continuous high-speed rotation, extreme temperatures, and steam impurities contribute to this deterioration, resulting in efficiency losses and higher maintenance costs.
Solution:
Triveni Turbines utilizes advanced 3D printing and scanning technologies for precise manufacturing and restoration of worn-out components. This approach minimizes downtime and extends steam turbine’s lifespan. By providing customized solutions, we enhance steam turbine performance while reducing unforeseen maintenance expenses.
Overheating and Thermal Fatigue
Prolonged exposure to high temperatures causes thermal fatigue, leading to cracks and material deterioration. Overheating can decrease efficiency and, in severe cases, result in unplanned shutdowns.
Solution:
Triveni Turbines incorporates advanced materials and innovations to design and develop high-efficiency steam turbines. Our sustainable power solutions leverage optimized steam flow and thermal coatings to minimize overheating risks. Additionally, regular monitoring and predictive maintenance ensure consistent and reliable performance.
Vibration and Imbalance Issues
Excessive vibrations in steam turbines stem from factors such as rotor misalignment, imbalance, or inadequate lubrication leading to premature component failure and reduced efficiency .
Solution:
Advanced steam turbine technology employs state-of-the-art dynamic balancing and precision alignment techniques to reduce vibrations and enhance operational stability. Expert service teams perform real-time diagnostics, detecting potential issues in the early stages to ensure seamless performance and greater reliability.
Steam Path Contamination
Foreign particles in the steam path, including corrosion byproducts and mineral deposits, can decrease efficiency and increase the risk of blade damage.
Solution:
Advanced filtration systems and specialized surface coatings protect against contamination-related damage, ensuring long-term reliability. Regular maintenance schedules and innovative aftermarket solutions further enhance steam turbine performance, maximizing efficiency and enabling cost-effective power generation.
Efficiency Losses Due to Ageing Components
Older steam turbines often experience efficieny losses due to outdated technology and material fatigue.
Solution:
Triveni Turbines is a leader in modernization and retrofit solutions, integrating the latest innovations into existing systems. Our energy optimization strategies improve steam turbines’ efficiency while supporting the global energy transition towards greener technology.
Overcoming steam turbine repair challenges requires proactive maintenance, advanced diagnostics, and precision engineering. Triveni Turbines is one of the leading steam turbine repair company, setting industry benchmarks with innovative technology, sustainable power solutions, and customized steam turbine upgrades. By focussing on energy optimization and reducing environmental impact, we enable industries achieve cost-effective power generation with a lower carbon footprint.